Frontier TechnologyAdditive manufacturing field is booming, technological innovation to lead the industry change Market research and analysis shows that the additive manufacturing field is experiencing rapid technological development, with numerous domestic and international technological achievements. As technological advances continue to drive change in various industries around the world, additive manufacturing is gradually gaining popularity. The global additive manufacturing market size is expected to reach USD 76.16 billion by 2030 and continue to grow at a CAGR of 20.8% between 2022 and 2030. In the face of growing downstream demand, countries have increased investment in additive manufacturing research and development, and related technologies are changing rapidly. On the domestic front, domestic backbone enterprises have successfully developed the world's first Tantalum-metal bone-filled reconstruction rods with their 3D printing solutions, and have been certified by the State Drug Administration. This breakthrough signals that 3D printed tantalum metal will be widely used in the future. Meanwhile, Chinese scientists have also successfully developed 3D printed titanium alloys with "anti-fatigue" properties, expanding new boundaries for aerospace applications. On the international stage, the introduction of advanced technologies by foreign companies has brought significant simplification of the additive manufacturing testing workflow. In addition, the application of 3D printing simulation technology is also expanding, providing strong support for solving problems in the additive manufacturing process.
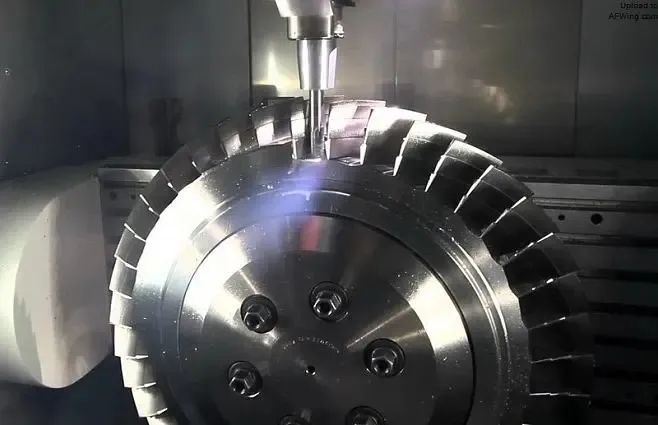
It is worth mentioning that the domestic backbone enterprises, in cooperation with medical colleges, have successfully developed the world's first 3D-printed bone-like structure tantalum metal bone-filled reconstruction rods by adopting advanced metal 3D-printing solutions, and obtained the registration certificate for Class III medical devices issued by the State Drug Administration. This is the domestic backbone enterprise in the help of medical industry partners to obtain the registration certificate of class III medical devices. Tantalum metal has a wide range of application prospects in the industrial and medical fields, and the core technology of 3D printing high density and high mechanical properties of tantalum metal mastered by the domestic backbone enterprises will have a positive impact on China's development in the development of high-end orthopedic implants, medical devices and refractory metal industrial parts. In addition, the relevant professional team of the Institute of Metals of the Chinese Academy of Sciences has also achieved impressive results. They successfully prepared 3D printed titanium alloy materials with high fatigue resistance, and the related research results have been published in the journal Nature. The researchers prepared a nearly porosity-free, near-beta-organized Ti-6-4 alloy through an innovative step-by-step defect and organization modulation process. This breakthrough technology will open up new possibilities for expanding applications in aerospace. The tensile-tensile fatigue strength soared from 475 MPa in the pristine state to 978 MPa, achieving a remarkable increase of up to 106%. This major breakthrough not only overturns the traditional perception of the fatigue properties of 3D printed materials, but also highlights the unique advantages of 3D printing technology in the field of anti-fatigue manufacturing. This innovation opens new doors for the widespread use of 3D printed materials as structural load-bearing components in critical areas such as aerospace. Meanwhile, the UK company's partnership with the mechanical testing solutions provider has revolutionized technological advances in the field of additive manufacturing. Together they have developed new technology that greatly simplifies the workflow of additive manufacturing testing, making it possible to directly test additively manufactured parts. This technology not only improves testing efficiency, reducing traditional testing time to five minutes, but also dramatically reduces the need for sample preparation, resulting in a significant reduction in mechanical testing costs.
Looking ahead, with the growing demand for additive manufacturing technologies in various industries across the globe, the global market size for additive manufacturing is expected to reach a staggering $76.16 billion by 2030 and grow at a CAGR of 20.8% between 2022 and 2030. Against this backdrop, U.S. companies in Japan are bringing a fresh perspective to additive manufacturing by combining simulation technology with additive manufacturing.

During the additive manufacturing process, predicting deformation is critical to ensuring successful part builds, reducing costs, and avoiding printing errors. Using multi-physics field simulation tools, U.S. companies are able to analyze and predict thermal deformation ahead of time and validate engineering dynamics by adjusting parameters to ensure structural integrity, address thermal issues, optimize fluid flow, and cope with impact. This innovation not only reduces material costs, but also optimizes additive manufacturing services and expands the customer base for 3D printing.